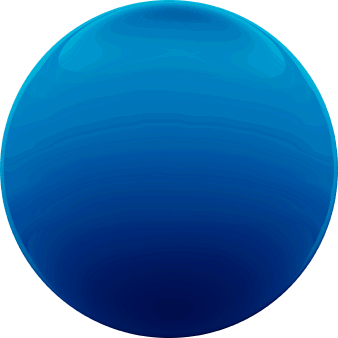
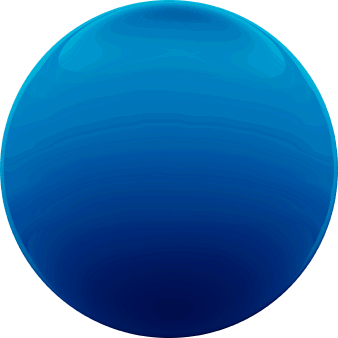
Sheet Metal Fabrication
and Forming
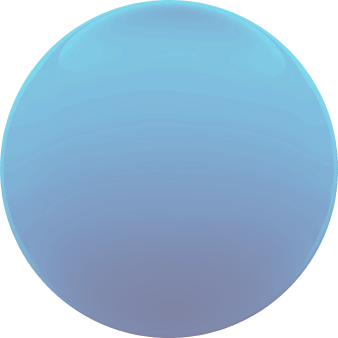
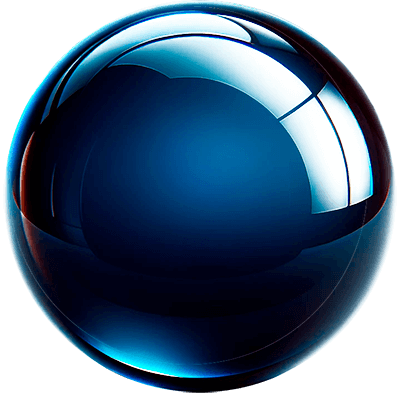
Sheet metal fabrication can transform detailed concepts into durable, functional realities. Whether it’s a sleek enclosure or a complex part, we form our clients’ ideas into durable, functional metal solutions that power their projects forward. Are you ready to see your concepts realized with unbeatable precision and skill?
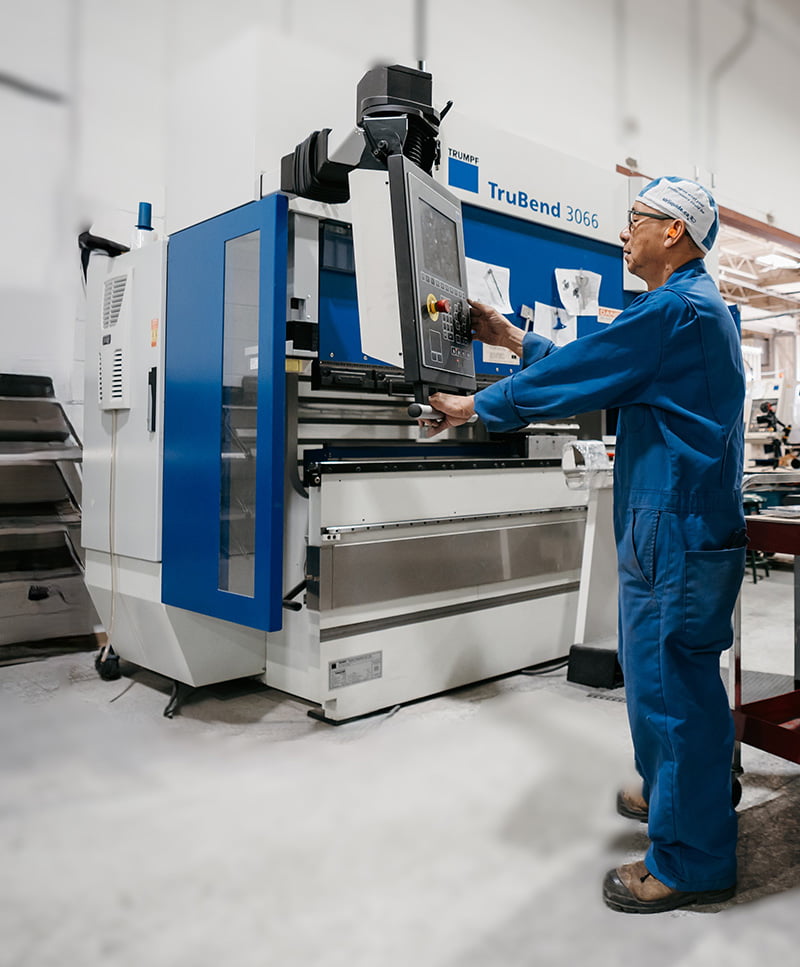
Cutting-Edge Fabrication for Any Design Challenge
Blending traditional craftsmanship and modern technology, IMS can transform humble sheet metal into detailed, functional components tailored to the most exact needs.
Laser Cutting and Punching
Precision cuts and powerful punches. We transform metal sheets into perfectly shaped parts using our top-tier laser cutting and punching technologies. Whether you need robust components or intricate designs, we’re here to make it happen.
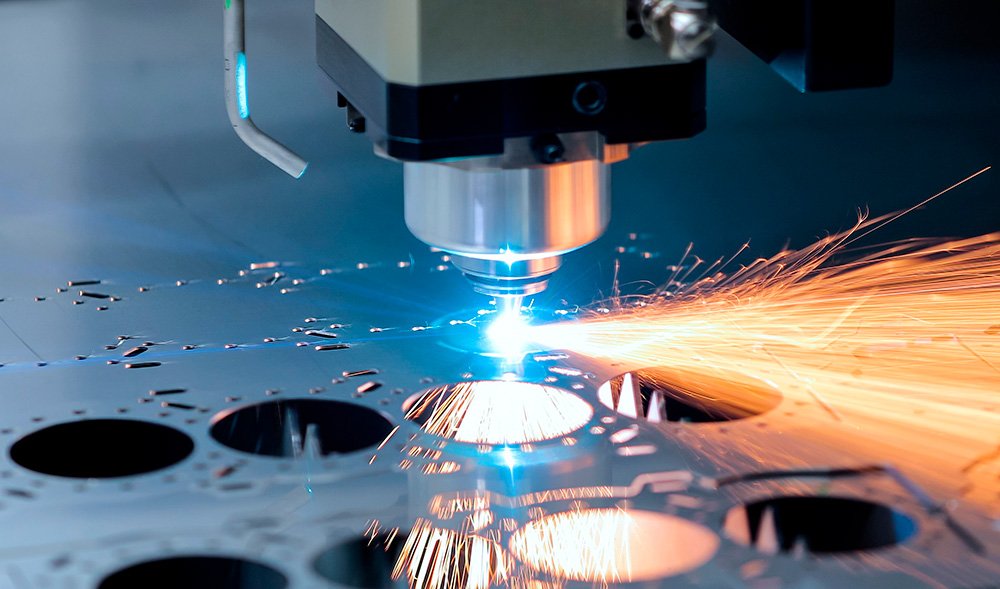
Welding
High-quality joints for durable construction. At IMS, we fuse expertise and technology in our welding operations. Our skilled welders excel in MIG, TIG, and spot welding, each offering distinct advantages depending on your needs.
We choose each welding method to match specific project requirements, ensuring durability and strength. Trust us to deliver components that exceed the rigorous demands of your applications.
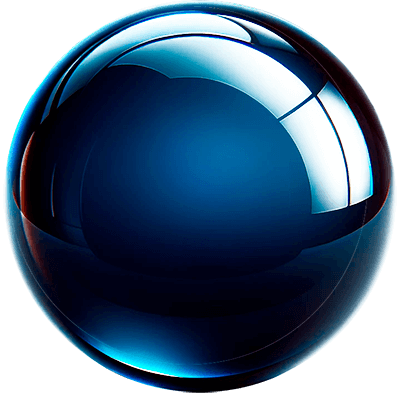
MIG Welding
The MIG welding process uses a continuous wire feed, combining speed with efficiency to produce clean, strong welds on various metals. This method is perfect for heavy-duty projects and delicate custom work, ensuring a flawless finish with minimal cleanup.
TIG Welding
When perfection is paramount, TIG steps in with its high-quality welds. This technique is best for welding critical joints and intricate designs, offering unmatched accuracy and minimal heat input, essential for thin materials and complex assemblies.
Spot Welding
Our spot welding services provide efficient solutions for sheet metal fabrication, creating strong bonds with minimal processing time. It’s particularly effective for joining thinner materials where minimizing heat exposure is crucial to maintaining the integrity of the components.
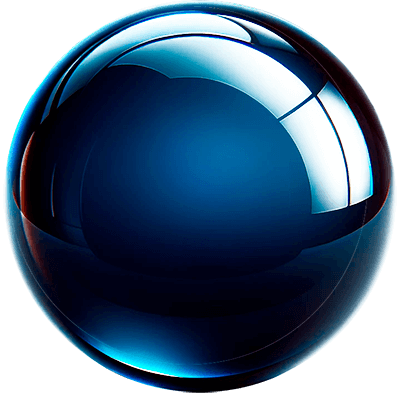
MIG Welding
The MIG welding process uses a continuous wire feed, combining speed with efficiency to produce clean, strong welds on various metals. This method is perfect for heavy-duty projects and delicate custom work, ensuring a flawless finish with minimal cleanup.
TIG Welding
When perfection is paramount, TIG steps in with its high-quality welds. This technique is best for welding critical joints and intricate designs, offering unmatched accuracy and minimal heat input, essential for thin materials and complex assemblies.
Spot Welding
Our spot welding services provide efficient solutions for sheet metal fabrication, creating strong bonds with minimal processing time. It’s particularly effective for joining thinner materials where minimizing heat exposure is crucial to maintaining the integrity of the components.