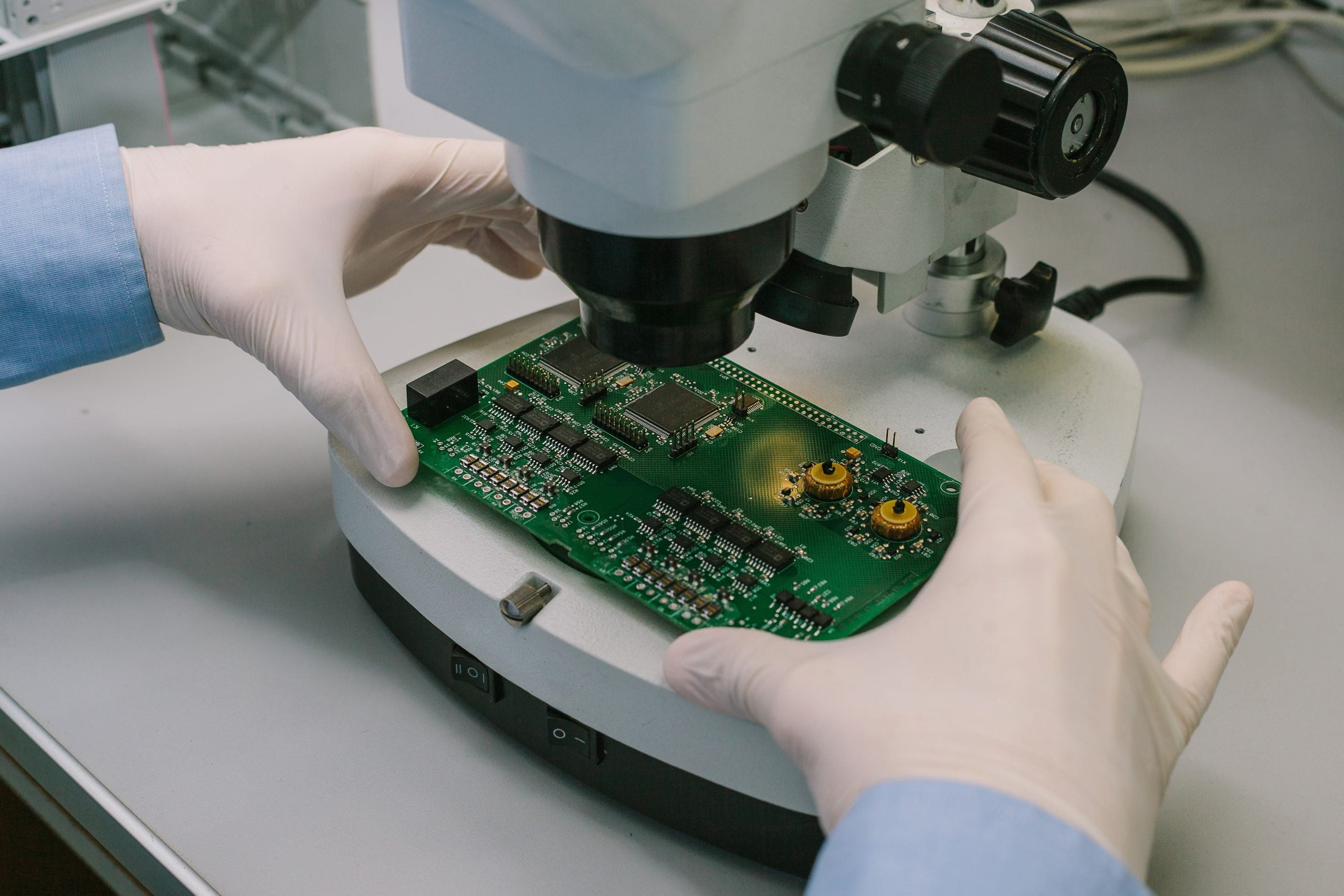
Quality is the cornerstone of success in electronics manufacturing. Whether it’s the smartphone in your pocket, the medical device that saves lives, or the automotive system that ensures safety, every product’s reliability hinges on meticulous quality control. This article explores the critical role of quality control in Electronic Contract Manufacturing Services (ECMS) and explains why choosing a partner committed to excellence, like IMS, makes all the difference.
Understanding Quality Control in ECMS
Quality control in electronics manufacturing is a comprehensive approach to ensuring that products meet specified standards and perform reliably. This involves a systematic process of checking, testing, and verifying that each product meets the required specifications.
Effective quality control systems integrate several components:
- Incoming Material Inspection: Ensures the raw materials and components meet strict quality standards before production begins.
- In-Process Quality Control: Continuous monitoring during the manufacturing process to catch and correct any issues in real time.
- Final Product Testing: Comprehensive testing of the finished products to ensure they comply with industry standards and client specifications.
- Regular Audits: Conducted to maintain and improve quality standards, ensuring ongoing compliance with certifications such as ISO 9001 and IPC-A-610.
A robust quality control framework directly impacts product reliability and customer satisfaction by minimizing defects, reducing rework costs, and enhancing overall product performance.
Essential Quality Control Processes in ECMS
Incoming Material Inspection
The foundation of quality control begins with the raw materials and components. Ensuring the quality of these inputs is crucial to preventing issues later in the production process. Techniques such as X-ray fluorescence (XRF) and automated optical inspection (AOI) are used to verify that incoming materials meet strict quality standards.
In-Process Quality Control
Real-time monitoring and control during the manufacturing process are vital to maintaining product quality. Methods like Statistical Process Control (SPC) and automated testing systems continuously assess quality throughout production, allowing for immediate corrective action when deviations occur.
Final Product Testing
Thorough testing of finished products ensures they meet industry standards and client specifications. This phase includes functional testing, environmental stress screening (ESS), and compliance testing to validate the product’s performance and reliability.
Quality Audits and Certifications
Regular audits are conducted to maintain and enhance quality standards. Certifications such as ISO 9001 and IPC-A-610 provide benchmarks for quality, ensuring that manufacturing processes align with international standards and best practices.
Benefits of Rigorous Quality Control in ECMS
Implementing rigorous quality control measures in ECMS offers numerous advantages:
Enhanced Product Reliability and Performance
Consistent quality control ensures that products perform reliably throughout their lifecycle. This leads to fewer failures and higher customer satisfaction.
Reduction in Defects and Rework Costs
By identifying and addressing defects early in the production process, the need for costly rework and repairs is significantly reduced, saving time and resources.
Increased Customer Satisfaction and Loyalty
High-quality products build trust and loyalty among customers. Satisfied customers are more likely to become repeat buyers and recommend your products to others.
Competitive Advantage in the Market
Companies known for stringent quality control practices stand out in the competitive market. This reputation for quality can be a key differentiator that attracts more clients.
Long-Term Cost Savings
Efficient quality control processes lead to fewer recalls and warranty claims, resulting in significant cost savings over time. Investing in quality control upfront reduces long-term expenses and enhances profitability.
Choosing an ECMS Partner with Strong Quality Control
Selecting the right ECMS partner is critical to the success of your project. Here are some essential factors to consider when evaluating an ECMS provider’s quality control capabilities:
Transparency and Traceability
Ensure the provider’s quality processes are transparent and traceable. This means having clear documentation and records of quality checks, inspections, and audits. Transparency builds trust and ensures accountability throughout the manufacturing process.
Track Record and Customer Feedback
Assess the provider’s history and customer reviews to gauge their reliability and performance. Look for case studies, client testimonials, and references highlighting the company’s commitment to quality and its ability to deliver consistent results.
Commitment to Continuous Improvement
A provider dedicated to continuous improvement consistently maintains high-quality standards and evolves with industry advancements. Look for evidence of ongoing training, process enhancements, and feedback mechanisms demonstrating their dedication to continually improving quality control practices.
Certifications and Industry Standards
Ensure the ECMS provider holds relevant certifications, such as ISO 9001:2015 and IPC standards. These certifications demonstrate the provider’s adherence to international quality and safety benchmarks, confirming that their processes meet rigorous standards.
Communication and Collaboration
Effective communication and collaboration are crucial for a successful partnership. Choose an ECMS provider that values transparency, responsiveness, and teamwork. Their ability to work closely with your team throughout the project lifecycle can significantly impact the quality and success of the final product.
Scalability and Flexibility
Your ECMS partner should be able to scale production up or down based on demand. Assess their capacity to handle varying production volumes and their flexibility in adapting to changes in project scope. A scalable and flexible partner can help you respond effectively to market fluctuations and growth opportunities.
Financial Stability
Ensure that the ECMS provider is financially stable. A financially healthy partner is better equipped to invest in new technologies, maintain high-quality standards, and support your project through to completion. Assess their financial health to ensure they can sustain long-term collaboration.
Geographic Location and Logistics
Consider the geographic location of your ECMS partner and its impact on logistics, lead times, and supply chain management. A partner operating in a region with reliable infrastructure and proximity to key suppliers can help streamline production processes and reduce shipping costs and lead times.
IMS’s Commitment to Quality Control
At IMS, quality control is more than a process—it’s a core philosophy embedded in every production stage. We are dedicated to delivering products that meet the highest standards of excellence, ensuring reliability and performance that our clients can trust.
Here’s how we uphold our commitment to quality:
Advanced Inspection Techniques
IMS employs cutting-edge inspection techniques such as X-ray fluorescence (XRF) and automated optical inspection (AOI). These methods allow us to detect and address any issues early in the production process, ensuring that every component meets stringent quality standards from the outset.
Rigorous In-Process Quality Control
Throughout the manufacturing process, IMS utilizes Statistical Process Control (SPC) and automated testing systems to continuously monitor product quality. This real-time assessment enables immediate corrections, ensuring that each product adheres to our high standards without compromising efficiency.
Comprehensive Final Product Testing
Before any product leaves our facility, it undergoes thorough testing to verify its performance and reliability. This includes functional testing, environmental stress screening (ESS), and compliance testing. These tests ensure that all products meet industry standards and client specifications, guaranteeing their performance in real-world conditions.
Quality Audits and Certifications
IMS conducts regular quality audits to maintain and enhance our quality standards. Our certifications are more than badges—they’re promises. IMS adheres to rigorous principles, ensuring each operational phase aligns with international quality and safety benchmarks.
Our ISO 9001:2015 certification demonstrates our commitment to maintaining the highest quality management standards, with annual audits reaffirming our adherence to these principles. Additionally, we build all products to at least IPC Class II standards and can meet Class III standards upon request, reflecting our dedication to excellence in electronics manufacturing.
Continuous Improvement
At IMS, we embrace the philosophy of continuous improvement. We are guided by our commitment to meet or exceed the expectations of our customers in all aspects of Contract Manufacturing Services. This principle drives us to regularly review our processes, incorporate feedback, and enhance our quality control measures. Our dedication to continuous improvement ensures that we remain industry leaders, consistently delivering exceptional products.
Client Testimonials and Case Studies
Our clients consistently highlight IMS’s reliability and dedication to quality. Our clients’ testimonials underline the success of our quality assurance practices, showcasing how we have helped clients achieve their goals through our meticulous quality control processes. One-year manufacturer’s warranties on all workmanship further underscore our commitment to delivering exceptional-caliber products.
The IMS Edge: Excellence in Every Detail
Success is engineered into everything we create, making each product a true reflection of our commitment to excellence. Our approach is characterized by:
- Solid Service: Personalization at every project stage, tailoring solutions to fit unique requirements, and guiding initial concepts to reality.
- Solid Quality: Setting new standards in quality through advanced technology, ensuring every detail exceeds expectations and reflects superior performance and reliability.
- Solid Product: Meticulous attention to detail—from rapid prototyping to full-scale production—ensures products meet expectations and introduces innovation that sets projects apart.
Ensuring Superior Quality in Electronics Manufacturing with IMS
Quality control in Electronic Contract Manufacturing Services (ECMS) is paramount for ensuring product reliability, customer satisfaction, and long-term success. By understanding the critical role of quality control and choosing a partner committed to excellence, companies can achieve superior results in their manufacturing projects.
IMS stands out as a leader in quality control, offering advanced inspection techniques, rigorous in-process monitoring, and comprehensive final product testing. With IMS, you benefit from a philosophy of continuous improvement and a commitment to delivering exceptional products that meet and exceed expectations.
Ready to elevate your manufacturing process? Contact IMS today and gain a partner that puts quality first. Let us help you bring your innovative products to market with confidence and precision.